What is the difference between OEE and month?
Often it is common to hear the phrase "we need a month." Although in some segments this need is real, it is essential to understand exactly what this solution does and if we are acquiring the right solution. Before we take any conclusion, it is essential to understand that Mes (Manufacturing Execution System) and OEE (Overall Equipment Effectiveness) are two distinct solutions used in industry to improve efficiency and operational performance.
Mes is a production control system that manages the execution of real -time manufacturing operations. It is designed to monitor and control manufacturing processes, track raw materials, manage quality, program production, among other functions. By providing real -time visibility of manufacturing operations, MELA helps companies optimize processes, improve efficiency, reduce costs and ensure regulatory compliance.
Its definition has changed a lot over the decades, adding management and control layers within its scope. If we are to evaluate this framing under the unique evaluation of the International Table, the forerun with the evaluation of this type of system, we will note that this definition already has 4 definitions historically. The higher the scope required as month, the greater the complexity, the prior data work and effort in the definition of processes and involvement of different areas of the company.
However, even with the possibility of managing multiple facets of productive execution, many companies inadvertently seek a month solution to treat a central theme in any industrial environment: the productivity of their resources. Behold OEE and solutions with focus on it arise.
Essentially, OEE is a metric that evaluates the overall effectiveness of the equipment in a production line. It takes into account three main factors of efficiency: availability (time when the equipment is available for production), performance (actual production speed compared to the ideal speed) and quality (percentage of products produced correctly). OEE is used to identify opportunities to improve machine productivity, reduce inactivity time, increase production and improve product quality. The implementation of a real -time, OEE -focused and highly automated productivity system is, in turn, much simpler and faster.
If you seek to get the maximum key resource productivity of your production through the 3 commented pillars, monitor your production in order to understand your actual capacity of each product and center, as well as identify inefficiencies and their causes on each machine or post, an OEE solution is the most effective.
However, if you have a very high criticality in equipment maintenance management, you need to improve material traceability at a level above than your ERP allows and/or seek a solution that has specific and advanced quality management features, you should look for a Mes solution. This solution can be from market or even internal industry development of these features on top of an OEE -centered previous solution, as materials, maintenance and quality scopes can often be very specific to each company.
In short, the confusion between these two solutions arises around the scope and focus of each, which can result in mistaken expectations about their features and goals. For example, implementing a month may improve the overall efficiency of the operation, but it will not necessarily automatically guarantee an increase in OEE. Similarly, improving the OEE of a specific machine may not solve broader production management problems a month could address.
Therefore, it is crucial to understand the distinctions between month and OEE and to recognize that each plays a different role in improving efficiency and operational performance in industry. Choosing the right system to meet specific needs and achieving the desired results is essential for business success.
If you are interested in implementing OEE in real time in your industry, get to know Evocon and see how this technology can help you!
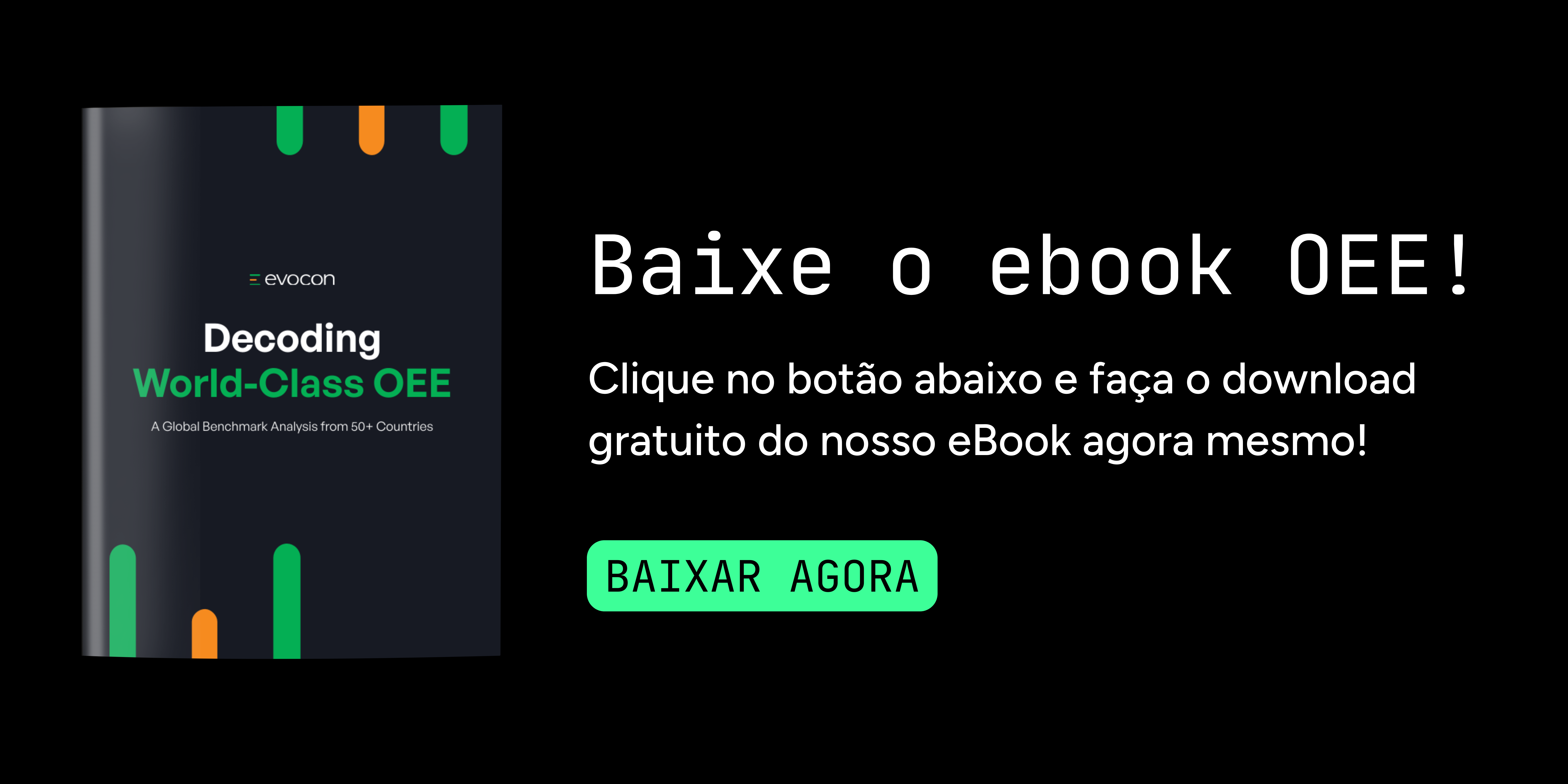