The challenge of the delivery date promise
Production and delivery dates when we work with industry, we see many productive systems guidelines: Make-to-Stock, Make-To-Rader, Assembly-to-Rader, Engineering-To-Rader (Project Against Order), as well as hybrid systems that mix these different guidelines. It is very normal for some industries to choose products that have a lot of demand and extensive life cycles to be produced for inventory in order to decrease lead-compliance lead teams and gain productive efficiency, while personalized products, which do not have much continuous demand or have a very short life cycle (case of fashion industry) are produced against order. In order not to generate obsolescence or high inventory costs, the Make-To-Rader (MTO) challenge is to quickly deliver its products from the moment a customer generates a order, without harming productive efficiency and, perhaps even more important, without delaying its delivery! Being very clear, the fact is that we have two delivery dates: which the customer wants to receive the product and the industry is committed to deliver it. Often these dates are quite different from each other. There are cases where you do not have the choice of choice and the customer will define the delivery date that the supplier must meet from market requirements and standards. But there are still cases where there is a dialogue between companies to define a definitive delivery date. This is where PPCP plays a crucial role for the best customer service (or at least it should play this role). The promise to define a delivery date that is performed by production, the ideal is that the PPCP/PPCPM area is responsible for such, as it is the area capable of analyzing all production variables (current production volume, materials, available resources, shifts, tools, etc.) to see when and how these orders can enter production. In many cases we see companies working with fixed lead teams for promise of delivery date, sometimes with standard values for any and all products. However, reality shows that each product has manufacturing itineraries and specific needs, which can make one product produce much faster than another, making no sense to both have the same deadline. Therefore, it is recommended that the areas of method and process engineering analyze and classify the products properly according to their productive effort. It is not problematic to work with fixed lead teams per product family and, if the products are similar, at the limit, it is also not wrong to have a fixed lead time for all your products. This can be a facilitator for the very interesting commercial area. However, the PPCP needs to analyze these requests that arrive for production, needs to validate their delivery within the deadline and contingency processes for delays must exist. If a order that arrives without delivery date and the PPCP will define it and will pass to the commercial area to transmit to the customer, ie an order that already comes with a delivery date and the PPCP confirms whether or not to deliver that order, this area does a reality. From the factory (s), otherwise we will be making a promise that we do not know if we can fulfill. And there is nothing worse for the image of a company, as well as product quality factors, than not fulfilling delivery deadlines. Promise what you can do is at these times that technological contribution can give us the necessary backing so as not to generate unnecessary delays and disorders. To have a good delivery date promise process, we need to have two things very well implemented and internalized by the areas of industry: an agile communication and information process between the commercial and PPCP area, adhering to the company's commercial characteristics (1), as well as an accurate and reliable production programming system that can well evaluate productive variables (2). width = "547"]
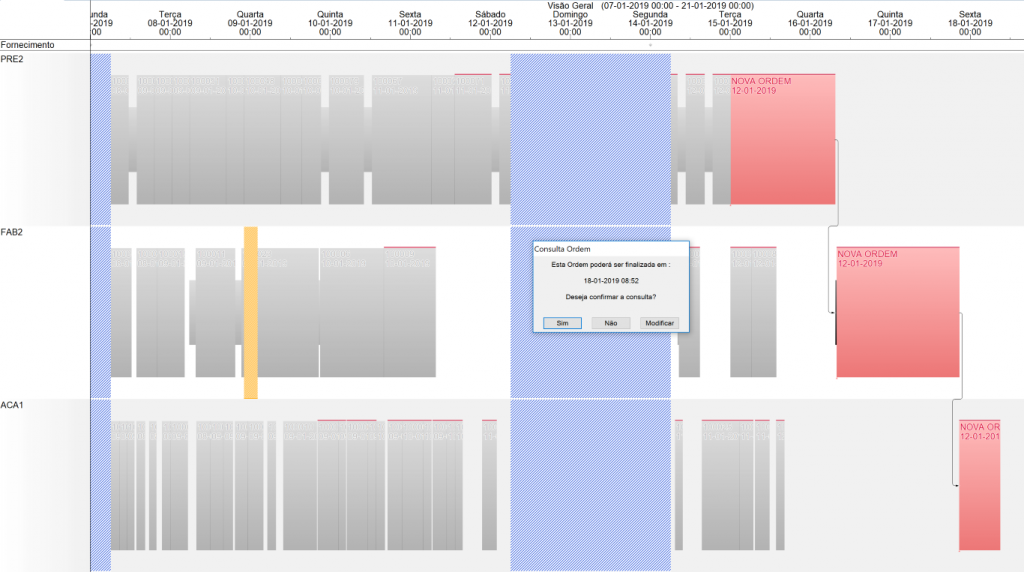
Viable Delivery Date Consultation in PREACTOR Software APS [/Caption] to establish this process of the first point raised you need to understand whether the market needs immediate responses to the demands or if it is possible to standardize a process with timeline to perform mass order analysis. For the first case a higher level of automation is required, as orders will arrive in a dispersed manner over time and need a quick and individualized return, making PPCP participation more concentrated in generating business rules so that this system occurs without having a person on the team available all the time to promise deadlines. For the second case, where one or two shift deadlines can be worked for the return of information, you can create a process with greater involvement between the scheduled areas and simulations to generate the delivery dates of all orders received in a time window. This allows, in case of not being able to produce everyone, or that the factory programming has more profoundly modifying to meet any need, a much -aligned dialogue and consensus can occur between commercial and PPCP to make decisions. As for the second important point, relating to a reliable system for production programming, it is essential to take into account that the factory (s) has a finite, and it is not decipherable. Only with water load analyzes/man, but we need a system capable of treating the most different possible variables, from available machinery to produce, synchronization between productive operations, to critical tools of tools, labor or even physical space. Otherwise, confirming an order by looking at a spreadsheet or playing a coin has the same effectiveness. To know what systems can be and how they work, learn more about the PREACTOR APS and contact neo !