Planning vs Programming: What is the role of APS?
Do you know the role of APS ? There are basically two major processes covered by PHC, planning and programming. And with many advantages , due to the fact that it allows the long -term short -term production plans to go through the entire production chain and considering virtually all the variables and restrictions of the productive environment. Some terms may be related to the same subject, such as fine production planning software or finite programming systems, as well as “ Advanced Planning Systems ” in English. See more about the origin of APS ! If we analyze the main processes of supply chain management , we will find the configuration below, where it is possible to identify where the solutions focused on planning and programming are fitted.
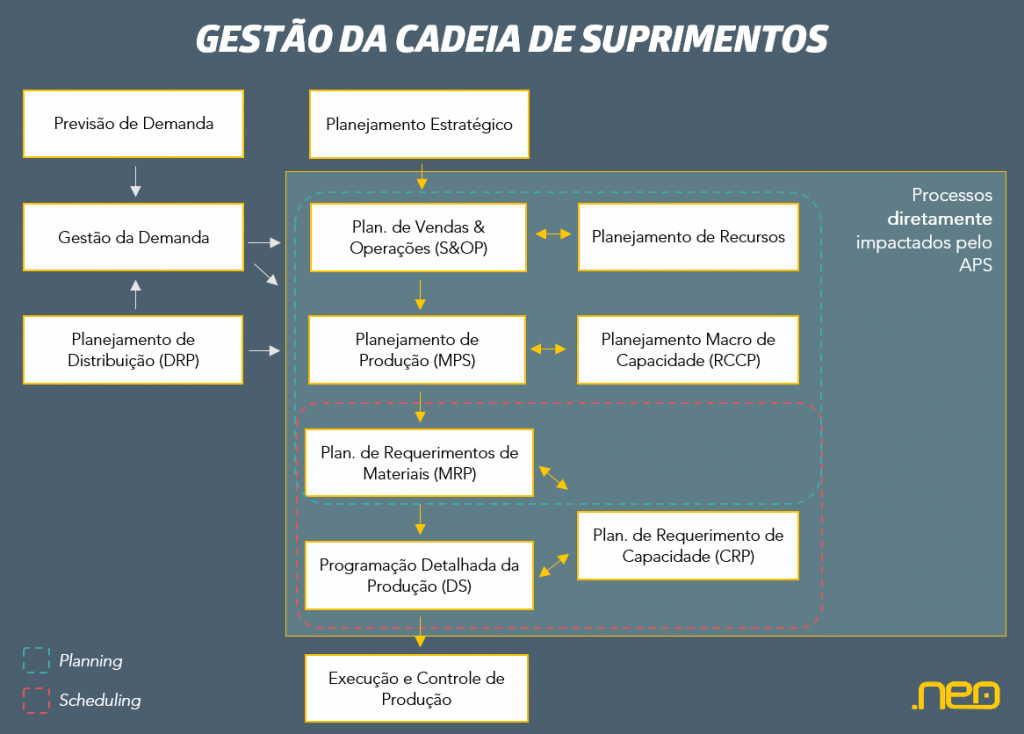
Supply Chain Management (Supply Chain) and APS [/Caption]
Production planning with APS
APS solution has an exclusive focus on detailed production programming processes (their first versions did not contemplate planning, or at least not finite capacity, causing the APS concept perception to be linked only to the Fine Programming - Scheduling ), but a complete APS covers much more than that. production planning process basically has the objective of defining what to produce in each planning period and in what amount, what is represented by the Master Production Plan. It is based on the actual and/or expected demand for each period of a horizon, and may vary from weeks to months, and the inventory and service policies that each product has (these policies end up being used mainly by companies that produce for inventory, but companies that also need to make their planning). Process is usually performed through ERP software themselves which, as we have seen, have their limitations on the restriction of productive capacity to generate these production plans. As in planning we work with a more macro and less detailed view of resources (it does not necessarily matter, how that production will be performed within each shift and each day, but how much it will be produced in that week of each product), these limitations are therefore less critical. If any business rule is necessary, if the bottlenecks can be dynamic, or if the variety of volume of skus is very high, other restrictions not easily managed by by ERPs may arise. Remember that the planning process (in English usually attributed to Master Scheduling), by definition, is after S&OP, sales planning and integrated operations (Sales & Operations Planning). Even so, it can closely relate to APS for two reasons: first, by the S&OP characteristic of using a long horizon, which generates a greater need for scenario simulation in the face of future uncertainties; As well as resource planning, which interacts with S&OP and needs to see productive capacity. As the APS has all its dynamics based on this generation of scenarios and capacity management, it can greatly support collaborative sales and operations planning. The difference in how the APS will act in each of these two processes, basically consists of the granularity level of each one, both for its position in the supply chain process cycle, as for your goal. CharacteristicsSaps (Planning) -> S & OP
PHS (Planning) -> MPS
Horizon
Horizon of 3, 12 or more months
Horizon from 1 to 3-4 months
Product Object
Sku
Management of restrictions to the most critical (s)
More restrictions
As long as S&P will see a longer horizon to support the tactical and strategic level, probably analyzing product families, MPS will work with a maximum -linked horizon accumulated supply lead time (ie the longest in time traced between purchase, production and delivery of a product ) . Only the most critical restrictions and work with family sales forecasts, which would later be disaggregated in SKUS (Stock Keeping Unit, or simply a product). This is enough, from a capacity point of view, the goal is to see how much it will be consumed by the expected volume of sales and if any action is required to modify it or review the sales plan. If we seek to support the MPS itself (Master Schedule), we will look at the level finished by SKU, which generates the formal MPs, and then we will explode this demand at the other levels of product structures to define what should be produced and purchased, assessing and bought. Impacts on capacity we can have in each planning period and taking actions to adapt capacity and demand during this period in question. In this process, simplifications that were made there in S&P can surface here, highlighting restrictions and idities that may have passed unnoticed and will have significant impacts on the operation. The explosion of material needs, characterized by the MRP/MRPII of the traditional bibliography, could be here only at the level of planning. However, we understand that, due to the dynamism that material management currently has, one can no longer think of MRP, even with finite capacity, without considering that it must support a short/medium term process, recalculating the needs from the revisions of plans that the fine programming performs. Therefore, he is encompassed in both solutions.
Production programming with APS
The Production Detailed Scheduling process is part of the volumes to produce previously defined in MPS, or simply on continuous demands of customer requests for MTO-to-Rader industry, with the objective of defining in detail when each demand will be produced and (this is the main critical point of this process) ". Or at least the main ones if the bottlenecks of these processes are stable and defined. Since APS raises the degree of accuracy of this process, we come to call it thin programming. Let's look at its elements. Before anything, it is important to know what will be programmed, what we call the programming object . Each company has its way of managing it, but the most standard nomenclature is the production order (OP) or manufacturing. It was created from the MPS we saw earlier, or even by the MRP. However, an OP is not just a reflection of net needs from MPS and MRP. Here should be applied production policies, such as minimum, multiple and maximum lot information allowed by the industrial area for the execution of each process. That is, MPS can generate a need for production of 5000 units from a product for a given period, but if the maximum lot is 2500 units, we will have two production orders. CASE APS receives a production order of 5000 and we need it to divide it, it is fully viable to perform this division. However, the complexity to manage the integrity of information between systems, needing to explain to the system that controls production or the ERP itself that that order has been divided and now each can follow a different path and need to be managed individually, makes it more efficient to perform this division in its origin, that is, in the generation of OP (in the system it is). Operative Post Really), according to distinct heuristics and simulations, depending on the goal ( why heuristics and not optimization?! ). With this, each feature receives its list of orders to be produced, with the exact sequence to be followed. How main characteristics of the classic APS for fine programming, can be highlighted:
- Finite capacity: In this case, the real skills of resources are considered, that is, work is allocated to resources only until its limit;
- Finite restrictions: To faithfully portray production, programming considers all operational restrictions existing in production, such as tool limitations, operators, matrices, gauges, electricity, among others;
- Use of sequence -dependent capacity: The way capacity will be consumed should vary according to the sequence, from the variation of internal setup times to the distinction of efficiency between machines capable of performing the same operation;
- Materials Management: The interdependence between production and material availability needs to be considered, seeing the stocks available for allocation in the production orders that will consume them, as well as the expected arrivals of more materials and the restrictions and priorities of allocation they can have;
- Relationship between Orders: Production orders can be interconnected in a static or dynamic manner, thus ensuring better control over production;
- Reprogramming: Due to unforeseen production and changes in production, these systems allow instant reprogramming in order to keep the entire company updated. This can be both in a weekly review of what will be produced in accordance with the other areas of the company, through S&E, and a punctual change due to an emergency;
- Scenario Simulations: Because it demonstrates the reality of the company's production, it is possible to simulate performance analysis and the costs involved with the use of overtime, outsourcing, equipment purchases, lot division, etc.;
Comparative summary between the two parts of an APS solution
[Caption Id = "Attachment_2696" Align = "AligNenter" Width = "1024"]
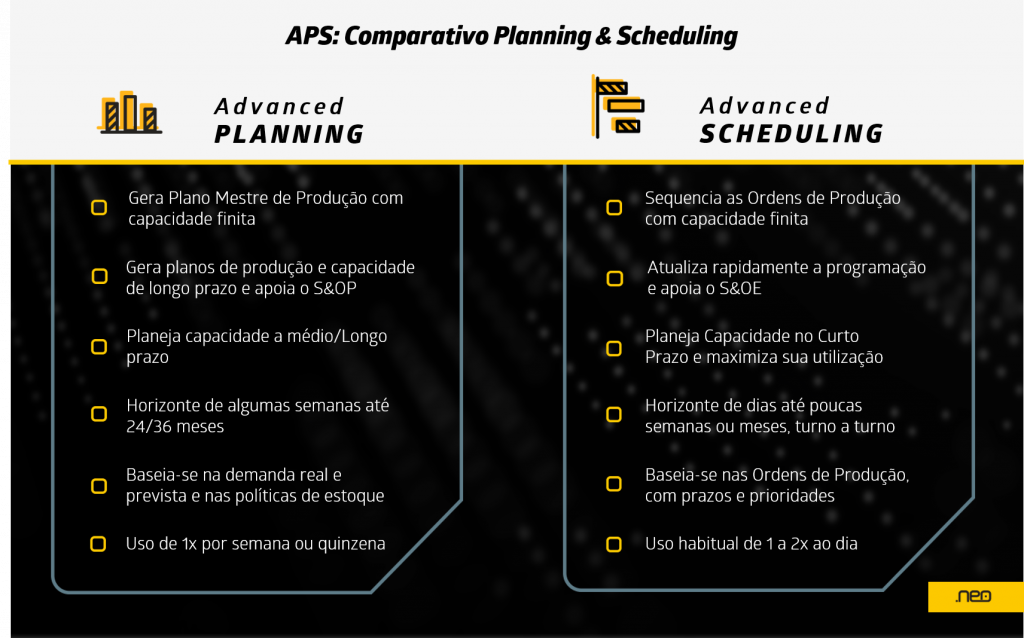
APS Planning and Scheduling [/Caption] evaluating the whole, we understand that today you already have enough technology to do an increasingly integrated process. There is no reason to make an MPs looking finite capacity with regard to the finished product, considering only a chosen neck, and then exploding other needs by MRP, without seeing other restrictions. So as we should understand that changes in demand and supply will occur and the need to redeem the flow in a fast and assertive manner is increasing. We did this in the 80's and 90s because there were no alternatives effective enough. Today is different. This evolution is not a quick process, but it is essential for those seeking to have agile and efficient supply chain management. But and then, would you like to know more about supply chain, PHC and other content? Accompanies Neo's Blog and see, in addition to this content, more information linked to Production Engineering . Prove and follow us on LinkedIn and other social networks to follow more news. [NOPTIN-Form ID = 2822]