Programming adherence: your dilemma and how it can be measured
Eliyahu M. Goldatt, one of the greatest production engineering gurus, has a famous phrase that says, "Tell me how I am and I will tell you how I will behave." Thus, adherence to programming plays a key role within production engineering.
It seems easy to understand, but when we talk about measuring industrial production, the application is not so simple. This is because there are conflicting management metrics. Today we are going to talk about one of them and their paradoxes, with a widely used indicator: adherence to programming.
What is adherence to programming?
It is a very useful indicator that can be interpreted in many ways, depending on the company and its refinement level. Some companies measure adherence only comparing the predicted or promised volume of production with the realization. This is a very superficial assessment that does not consider the effectiveness of using what is manufactured.
Even though it is a more used format by industries that work against inventory, because the service is less sensitive to variations in production, the risk is to damage the health of inventory and its turnover.
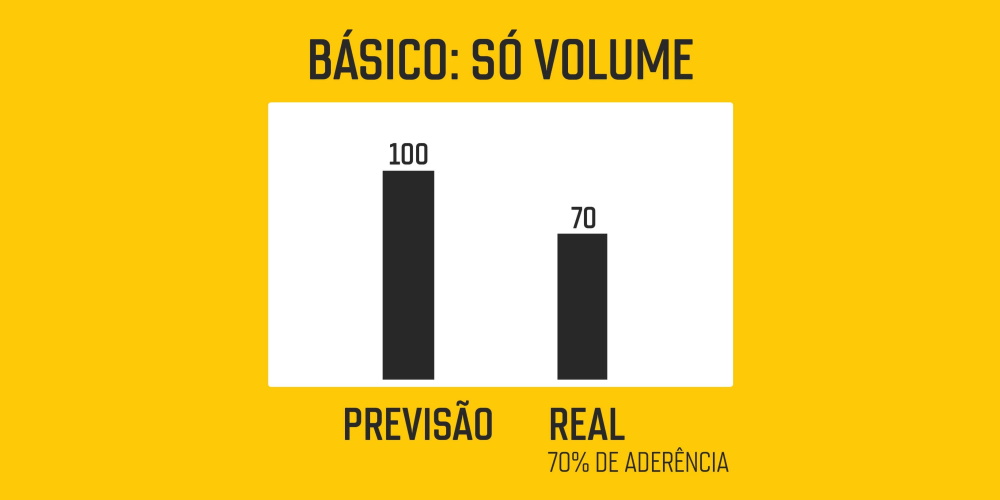
Probably the most common use is the one in which you look at the “predicted vs performed” relationship by SKU, it allows you to understand if the amount that had been programmed was produced. This is a useful vision, but often sabotaged by the way the industrial area is measured, usually by volume produced. This is because, often, what has been programmed is not the one that generates the most volume, because it is more difficult or time consuming to produce.
If a company bonuses its employees for volume production, more difficult items, but sometimes they may have a larger margin or are more strategic than the others, they can "suffer the penalty." The operator will be encouraged not to follow the logic of Fifo (First In, First Out) or Lip (Last In, First Out), but that of Miifo (Most Interesting In, First Out). Here comes the spirit of Goldatt to alert us!
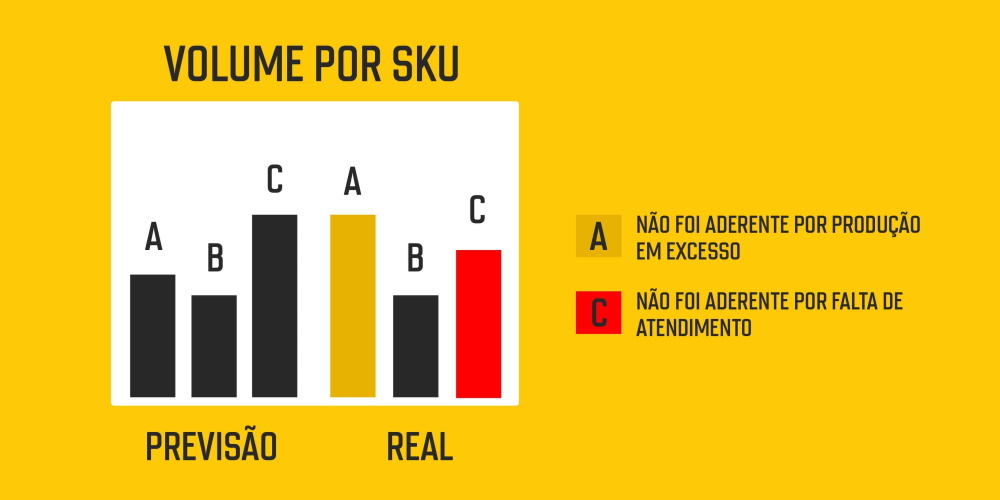
However, it is no use pivoting the evaluation to purely see the grip and charge a product mix of product, which it cannot meet. This is really a harder KPI to be assertive.
Comparing volumes turns out to be simpler, easily replicable empirically. Therefore, it is natural that it is one of the most widespread forms of evaluation for variable remuneration. We have to have confidence in the model when it is to move people's pocket.
It is precisely to bring this maturity to the adhesion indicator that there are APS solutions. Through them, viable and reliable plans can be created. Not only due to advanced rules and algorithms that are used, but because they are usually built along with the support of production, which knows the restrictions that the factory has.
Thus, the indicator gains a new meaning and importance and can really become the most effective means of control between PPCP and the industrial area. A daily frequency or adhesion shift is ideal for being more assertive, although you can start with weekly control.
There are still opportunities to gain refinement and robustness with this indicator when asking, "Did you do it in the volume of each item correctly, but in the right sequence? And in the right machine?" This measurement deepening can be very useful for those who have many operations to transform a product, and as a result a sequence change can have very negative impacts on later processes that were counting on the programmed sequence of their predecessors.
Schedule in different resources can also change not only efficiency- which may be different between machines- but also the cost of the product, if it is calculated considering the feature actually used for manufacturing and this is confronted with the planned cost for this item.
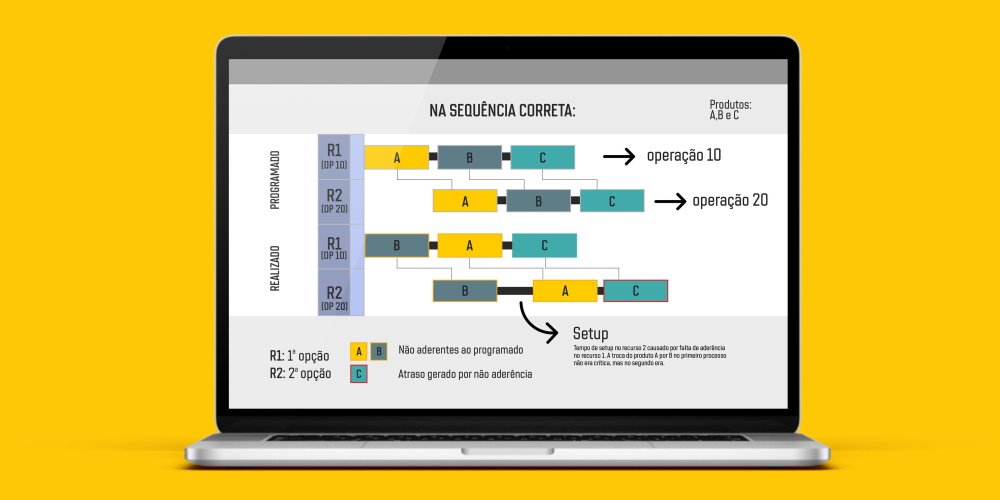
There are several ways to focus on the evaluation of the “predicted vs performed” from the moment the “predicted” is more assertive. And the consequence, is a management that does not only look at volume and maximization of asset use, but has a holistic view of the company, balanced efficiency with the level of service, considering the interdependencies between processes, strategic priorities of the company and thus creating the correct incentive.
Want to explore more about this subject?! industry cyborg episodes where we talked to Ricardo Lauri of the Lunelli group about the subject, and the conversation with Ariel Possebon of the producttare in which we also talk about restriction theory.
How can neo help your industry?
Neo Digital Industries is Siemens Smart Expert Partner and offers solutions with business analysis and implementation of APS software . We create a new concept that values technological avant -garde and technical excellence, while we believe in human sensitivity, creative work and personalized and committed relationship.
Contact the form below or our WhatsApp to learn more about our solutions and mark a personalized analysis for the needs of your business.