How do I integrate my logistics with PPCP?
In this text Carolina Pessoa, Neo's developer partner explains how to integrate logistics with PPCP (Production Planning, Programming and Control) is no longer an option and has become a strategic differential for the success of operations in the competitive market that is configured. To understand how it is possible to make this crucial integration, read the following article!
In the current scenario, marked by high competitiveness, complex production chains and increasingly demanding clients, integrating logistics into PPCP (planning, programming and production control) is no longer an option and has become a strategic differential for the success of operations.
However, in practice, it is still common for companies to maintain these areas working in isolation, which results in bottlenecks, communication failures, unbalanced stocks and often deliveries. The good news is that integrating logistics and PPCP is totally possible - and the path goes through well -defined processes, technology and a collaborative culture.
💡 Why is integrating logistics and PPCP so important?
When logistics and PPCP act in a synchronized manner, the company wins:
- Better predictability of production and deliveries;
- Cost reduction with storage and transportation;
- Greater efficiency in the use of resources;
- Flexibility to respond to unforeseen market;
- Increased customer satisfaction.
The integration of these areas transforms Supply Chain into a fluid gear, capable of generating value and increasing the company's competitiveness. And to achieve this level of excellence, more and more companies have been betting on specific digital solutions to connect their tip to end value chains.

🔍 How to do it?
The first step to integrating logistics with PPCP is to clearly map the company's information and material flows. This means understanding clearly:
- How information and data circulate between purchases, inventory, production and transportation;
- What are the critical steps in the logistics process;
- Where the largest bottlenecks and communication noises occur.
This mapping helps identify communication failures, locate logistics and operational bottlenecks, and standardize information between sectors, creating a solid base for alignment between the areas and an environment where everyone speaks the same "operational language".
Then it is essential that production planning is based on real and updated logistics chain data. This means that supply deadlines, inventory levels, transportation and lead teams need to be always visible and integrated with PPCP tools. When this information is treated in isolation, the risk of interruptions increases considerably.

📊 Planning based on real data
For efficient integration, PPCP must work with:
- Real supply deadlines;
- Lead Transport and Receipt Teams;
- Storage and movement capacity.
The more faithful this data integration, the lower the risk of delays and waste.

Another essential aspect is the use of integrated systems such as ERPs and supply chain specializing software. These tools allow logistics to feed real -time PPCP with data and output data, delivery status and input receiving forecast. Technology, in this sense, acts as the link between planning and execution, ensuring quick answers to unforeseen events.

💻 Technology as a link
Integrated management systems such as ERPs and supply chain specialized platforms are critical to connecting logistics and PPCP. They allow:
- Update and sharing of information in real time, such as inventory, orders and transport data;
- Automation of alerts and updates;
- Monitoring of Performance Indicators (KPIs).
Technology transforms the flow of information into an agile and reliable process.

In addition to technology, integration depends on a collaborative culture between teams. Without shared indicators, each area can work with conflicting priorities. Therefore, it is important that logistics and PPCP share clear objectives and common performance indicators, such as order service rate, logistical service level and adherence to the production plan. This helps reduce conflicts and guides decisions for what really matters: efficient service and customer value delivery.

🎯 Goals and indicators aligned
Without shared indicators, each area can work with conflicting priorities. Some essential metrics:
- Delivery rate on time;
- Stock turnover;
- Adherence to the production plan;
- Customer service level.

Another point that deserves attention is the joint planning of scenarios. Situations such as supplier delays, sudden increase in demand or logistics restrictions should be simulated and discussed in an integrated manner. This practice strengthens the company's reaction capacity, reduces the impact of unforeseen events and promotes more proactive management of Supply Chain. Anticipating problems and creating action plans is a practice that differentiates reactive companies from strategic companies.
Finally, it is important to establish a frequent alignment routine between the logistics and PPCP teams. Weekly or daily meetings, shared dashboards and clear communication are fundamental to adjust the plan according to the actual conditions of the market and the operation. Integration is not a punctual event, but a continuous process of alignment and improvement.
🚀 Empower your operation with Siemens solutions
To achieve these benefits, Siemens offers a powerful combination of solutions: SDL AX4 , a logistics collaboration platform, and Opcenter APS , an advanced production planning and programming system. Integration of these tools allows synchronizing delivery and receiving deadlines with production planning, quickly reacting to logistics or productive unforeseen events, and reducing communication failures between supply chain, production and transportation.
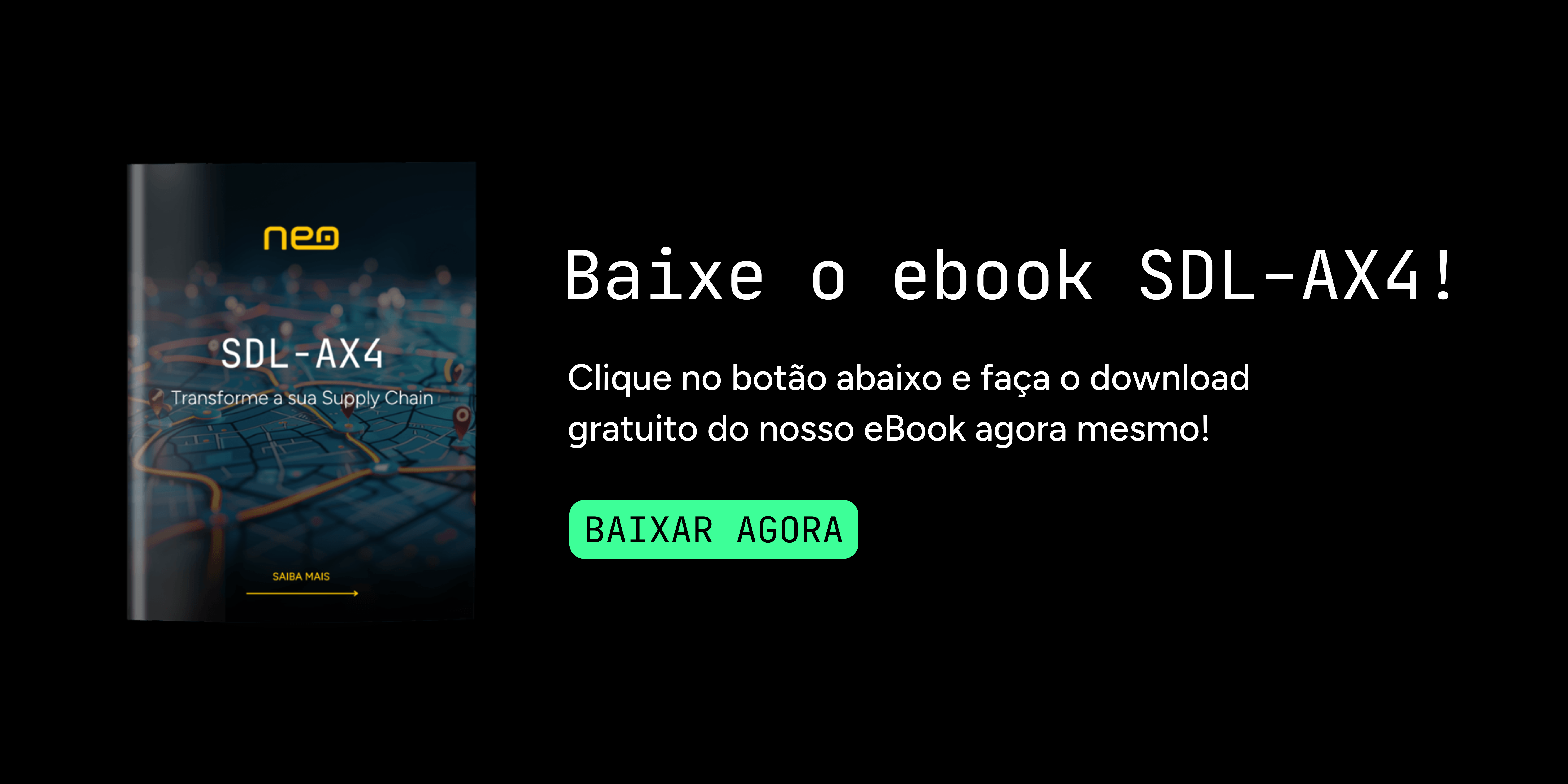
🧩 SDL Ax4 + Opcenter APS: Efficient Planning Integration to Execution
While SDL AX4 acts as a logistics hub, connecting suppliers, carriers and real -time distribution centers, Opcenter APS works to create intelligent and dynamic production plans, optimizing resources and capabilities based on real restrictions.
When fed with reliable logistics data, coming directly from SDL AX4 Opcenter PS planning becomes realistic and aligned with the reality of the logistics chain, capable of anticipating transportation and supply restrictions while providing flexibility for rapid adjustments without compromising deliveries. Together, these tools allow:
- Synchronize delivery and receiving deadlines with production planning;
- React quickly to logistical or productive unforeseen events;
- Reduce communication gaps between supply chain, production and transportation;
- Raise operational efficiency;
In the Siemens ecosystem, interoperability between SDL AX4 and Opcenter APS enables the sharing of logistics and real -time production data, reducing manual errors and rework and automation of warnings on time and capacity deviations. With SDL AX4 integrating logistics and Opcenter APS controlling production planning, information automatically flows between areas, strengthening data alignment and data -based decision making. From this integration, management is now guided by unique and reliable data.
%20(1).png)
✅ Conclusion
Integrating logistics and PPCP is a strategic step that allows you to turn challenges into opportunities, making your operation more efficient, agile and competitive. The synergy between planning and execution reduces costs, improves deadlines and generates real value for the customer. Thus, by joining robust solutions such as SDL AX4 and Opcenter APS , your company transforms planning and execution into a continuous and intelligent flow that can quickly adapt to market changes and ensure excellence deliveries.
👉 Request a personalized demonstration and find out how to increase the efficiency of your operation.
🔗 Click here and talk to a consultant