10 opportunities for industry PPCP 4.0
The Industry 4.0 subject is probably the most recurring theme in manufacturing companies today. The concept, which is so significant that it is classified as a new industrial revolution, presupposes an intelligent factory in which machines and systems are fully connected. In this article, we will address how PPCP can adapt and evolve to explore the opportunities generated by the evolution of manufacturing in the context of industry 4.0.
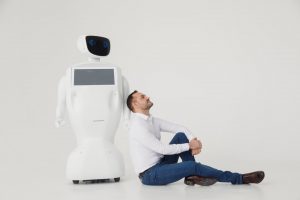
1. Autonomous programming and ideally artificial intelligence , all programming rules and criteria are already previously defined so that programming can be done completely autonomously. The programmer's interference must be minimal, preferably to be justified and compared to the previous automatic scenario to approve. If there are exceptional criteria that must be considered, they must be informed from system parameterizations but avoiding manual interference. If programming system rules do not consider all major variables, it is an indication that these rules need to be improved or the system needs to be reviewed. In an autonomous programming, every short time, the system is updated with the new orders and notes and reprogramming to the factory, keeping the team informed from smart notifications when everything is within the expected boundaries or sending alerts to the programmer. Thus, it is possible to make available the equivalent of a 24 -hour PCP and ensure the always balanced and updated programming for the factory.
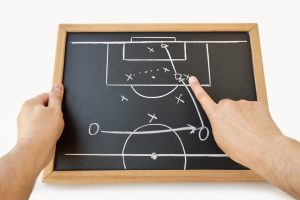
2. Total control over resources on the 4.0 industry PCP is not only the ability of some specific machines that is controlled and managed. On the contrary, all finite resources must be known and managed, including operators and tools. The workforce required to perform each operation should consider the variations of each type of product and machine, operators need to be defined according to their multi-functionality between different sectors and detailed labor availability should be considered, in some cases even integrating with the HR system and point clock. Thus, PPCP can guide to the factory the allocation of labor necessary according to the programming considering all the real characteristics and limitations of the process.
3. Factory without paper
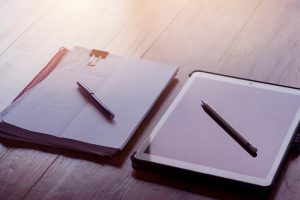
In industry 4.0 factory there is no more space for paper. Programming programming must be sent to the factory digitally. It is no longer acceptable to print the allocation of resources or a report with sequencing and deliver the paperwork to production supervisors. Instead, programming should be automatically released on screens similar to that of an airport or, when possible, sent to each machine's own terminal, focusing on the same environment the pointing and programming interface. Thus, changes can be made much more agilely, since it is not necessary to collect the old versions and reprint the programming when there is any change.
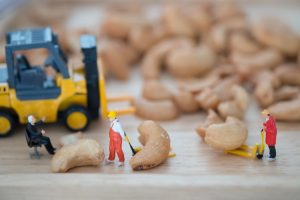
4. PPCP program -oriented movement , it is not just done the sequencing of the machines, but the movement is considered and even oriented by the production programming system. Programming criteria should already consider the physical location of resources and allocate the machines to minimize cross flow or unnecessary movements between previous and posterior resources that are distant from each other. In addition, the available programming can guide the movement, informing the subsequent feature to which the material must be sent after production. In some cases, the AGVs movement itself can be defined from detailed programming.
5.
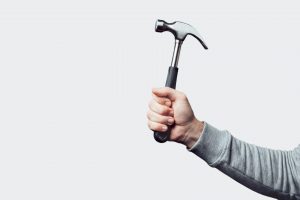
PPCP of the future does not work isolated. Interfaces with the main areas of the company are key to getting better performances. In this sense, an agile flow of information between PPCP and maintenance is critical. Ideally, when the operator registers a maintenance request on a particular equipment, PPCP should immediately receive this signal and depending on the type of problem (based on repair time history) already redistribute orders and rebalancing programming on alternative resources to minimize impact.
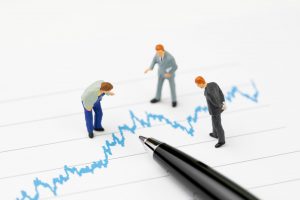
6. Machine Learning to identify patterns in the context of the connected factory, preference rules settings are no longer arbitrated or defined only by people's experience, but must be calculated based on machine learning algorithms so that the system learns to identify productivity gains patterns as it is more and more used. For example, from the first orders produced from a new product, the system can identify that production efficiency in some machines is much better than in others, and prioritizing the allocation of upcoming orders in the resources they have best performed in the recent past. Thus, the programming will be sent considering the machines with better performance for certain products (or molds, for example), without depending on the experience of people and a priority register that can quickly become obsolete.
7.
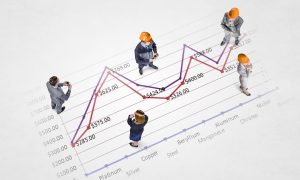
The main indicator of the factory of the future is the adherence of the programming. Instead of controlling production by units produced, which generates distortions for the variation of mix or unwanted priority behaviors, the main function of the factory will be performed all the programming with the least possible variation, since PPCP has already taken into account all the main variables and operational restrictions to ensure feasible programming and suitable for production strategies.
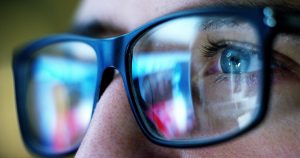
8. Agile reprogramming is not only production programming that must be agile, but reprogramming as well. In industry 4.0 PPCP, the planning system must be connected by reading the data from machine sensors, so that any performance variation can be rapidly updated and eventually recalculated. If there are refuse problems, lack of operators, or unexpected unavailability of raw materials, PPCP can quickly update itself digitally and reprogram the factory quickly trying to generate minimal impact.
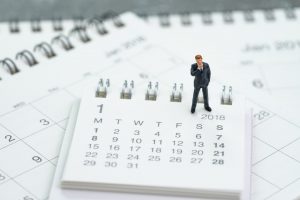
9. Real -time delivery promise in the context of industry 4.0, the delivery time promise process is also done connected with the factory. From a real -time consultation of the detailed production programming, the delivery deadlines for the new orders are made taking into account the detailed scripts of the products and the projected availability of the inputs. Even if it is launch products that are not yet registered in the ERP, the simulation can be performed from analogy with similar products or integration with script and structure of the PLM (Product Lifecycle Management) system).
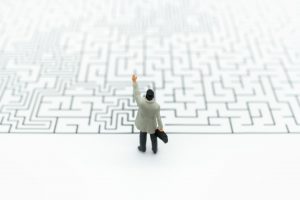
10. Advanced Planning of Scenarios are not only the production programming processes of production that can enhance and benefit from the advent of industry 4.0. Long -term medium planning can also and should be inserted in this contact. In this context, decision making is fully based on advanced scenarios, generating condensed and management information from thoroughly calculated data. S&P processes now consider the detailed capacity and real availability of all factory resources. It is no longer necessary to be limited to only 1 plan per month, at any time the system can connect the actual entry and updated factory situation to repress scenarios and write the directions throughout the month, all decisions are quantified and presented with financial integration for executive scenario analysis.
These opportunities are part of PPCP trends, but at the same time many of them are already realities in Neo customers. If you would like to better explore these points in your industry, contact us and take the next step in this industrial revolution!
[NOPTIN-Form ID = 2822]